A Look at Air Compressor Audits in Chemical Plants
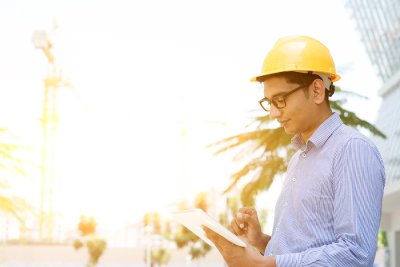
Considering the greater emphasis on safety, process stability, and system reliability within the chemical and petrochemical manufacturing industries, it’s no surprise that air compressor audits take on a more serious role in chemical plants than in other commercial or industrial settings. More than simply revealing when you need to seek air compressor repair in San Jose, regular air compressor audits can also enhance system reliability and reduce operating costs. Here are some important things you should know about air compressor audits in chemical plants.
Long Pipe Runs and Multiple Compressor Rooms
Auditing a compressed air distribution system in a chemical manufacturing facility is different than other industries for many reasons. For one, pressure drops can be an issue due to the typically extreme length of pipe runs, especially in remote areas of the plant. Some facilities get around this by having multiple compressor rooms, which can also be a challenge to audit considering how difficult it is to coordinate the behavior of systems with multiple entry points.
Demand and Supply Side Audits
Auditing the demand and supply side of the air compressor system inside a chemical plant first requires identifying the primary goal of the audit. For example, if increased reliability is the primary goal, the audit will look for areas of improvement or upgrades that will result in more repeatable performance of demand and supply control valves. Similarly, the goal of the air compressor audit may be to reduce operating costs.
Air Compressor Improvements
Although auditing chemical plants is a challenge, and investment, the potential return can be massive in terms of performance, reliability, and operating costs. Having as wide a view of an air compressor system as possible will allow an auditor to recommend areas where air compressor systems, processes, and/or components can be improved. For example, one common application in chemical facilities that often has a great potential for improvement is air sparging, in which compressed air is fed into a tank to reduce the concentrations of VOCs within the container.