Flow Metering in Large Air Compressor Systems
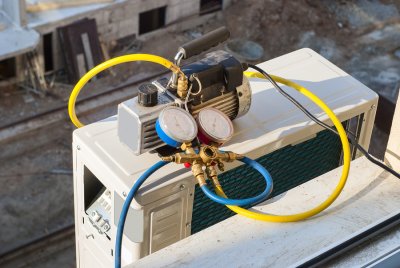
Achieving optimal pressure and flow in a compressed air system is important for minimizing maintenance and operating costs. When investing in a new industrial air compressor in San Jose, the first and most important thing is that you size the system appropriately for your specific production needs. After that, the process of maintaining system efficiency (and keeping operating and maintenance costs low) falls on your shoulders, or on the shoulders of whoever is tasked with overseeing the compressed air system. Flow metering offers significant opportunities to reduce energy costs and extend a compressor’s service life. Here’s what you need to know about flow measurement in large air compressor systems.
Thermal Mass Flow Meter
Although there are many different types of low-cost electronic air compressor metering instruments available, the most popular is the thermal mass flow meter (which is principally based on a design that dates back to 1914). Modern thermal mass flow meters provide accurate signal output without being affected by changes in air pressure or temperature, two factors that can affect the performance and accuracy of other flow metering devices.
Main Supply Header
When planning for the implementation of a flow metering device in your compressed air system, experts recommend compressed air flow meters be installed in the main supply header to provide the most accurate usage profile. It’s also recommended that a flow meter be installed somewhere in the delivery piping where the compressed air is clean and dry.
Non-Production Metering
When combined with electrical consumption readings, flow meters provide the basis for measuring the efficiency of an industrial air compressor. However, it’s important not to ignore measurements during non-production hours. Measuring flow during non-production hours can provide critical information on leakage rates or inappropriate uses of compressed air, such as blowing off workstations. Combining this information with your plant’s compressed air usage profile will allow you to achieve optimal system efficiency for lower production and maintenance costs associated with your industrial air compressor.